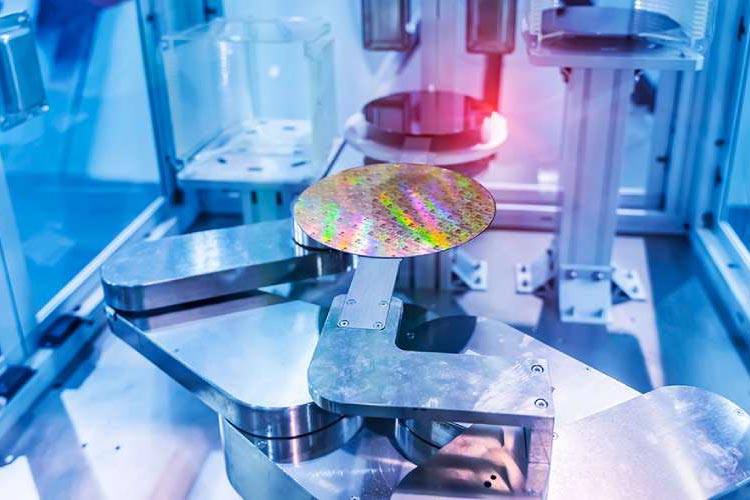
India lost the semiconductor growth race during the late 1980s. But, for the past five to six years, the government has unleashed various schemes, initiatives, and educational programs to boost chip fabs and design. Investments are happening, but there are a couple of grave impediments such as lack of proficient workforce and infrastructures. Currently, it is difficult to compete with countries like the USA, Vietnam, China, and South Korea as they have better policies, subsidies, and cost-efficiency. Apart from huge investment, chip fabrication units require gallons of pure water and uninterrupted power supply.
However, there is a constant price pressure from various international players, mostly China, which is forming an in-house semiconductor program by which 70 percent of locally manufactured chips will be used in all its products by the end of 2025. Industry experts from various associations have stated that India has done exceptionally well in the area of electronics manufacturing and chip design, but now it is the time to set-up more chip fabrication and manufacturing facilities.
Anurag Awasthi, Vice President, Policy, Government Corporate Relations at India Electronics and Semiconductor Association (IESA) said that skilling is always an important requirement to fulfill the goals of Atmanirbhar Bharat. He told CircuitDigest, “The important policies such as SPECS, DLI, and PLI will boost in-house design, manufacturing, and assembly. But, the point is self-reliance in manufacturing, skilling, distribution, and design. Amid the current subsidies proclaimed in Europe and in the US, and the unleashing of the CHIPS Act, Asia will dominate the global market as it has the expertise and the resources to control the volumes of semiconductor production. In an effort to boost economies of scale, a couple of global Asian firms are setting-up their production units in other countries, but it will take more time as the process is intricate and time-consuming.”
Awasthi added, “Europe and East Asia are now spearheading the R&D, South Korea and Taiwan dominating the manufacturing/OSAT, and China with a history of monopoly market leading the testing and packaging industry. The international value chains in this domain have crumbled. No country is a central location of all the semiconductor processes, and hence the hurdles in this sector are conspicuous.”
Why India Lost The Semiconductor Growth Journey During The Late 80s- A Historical Perspective.
In an article with the Statesman, Independent Journalist CHOODIE SHIVARAM said that before 1987 India was progressing in this sector at a large-scale and today, it should have its own semiconductor fabrication units. Now, the worst part is that the nation is twelve generations behind. There are some unforgivable reasons due to which India missed the bus numerous times such as bureaucratic lassitude, lack of leadership with a clear vision, improper infrastructures, and corruption. When the silicon revolution started happening during the early 1960s, Fairchild Semiconductor announced to set-up a fab, but bureaucratic fatigue helped them to move to Malaysia. A couple of months after the 1962 Indo-China war, Bharat Electronics Ltd. started a new fab to produce germanium and silicon based transistors.
The demand for these transistors were so high various global companies were lined up to place orders. This is when the cost-efficient integrated circuits (ICs) from Taiwan, South Korea, and China dominated the Indian market and BEL could not compete with the quality and price standards. Several fab units were forced to shut down. In the mid 1980s, there was another revolution in this sector when IISc professor A.R. Vasudeva Murthy in association with BEL formed Metkem Silicon Limited to manufacture polysilicon wafers for electronics and solar cells. Devoid of any proper policies, incentives, schemes, and lack of subsidized power, Metkem failed to manufacture top-notch polysilicon wafers.
Faisal Kawoosa, senior research analyst and founder at techArc said, “The point to be noted is that the country’s semiconductor journey already commenced way back in late 60s. Interestingly, Semiconductor Complex Ltd (SCL) was formed in Mohali in 1976 and started operation in 1984. Initially, the company started functioning with 5,000 nm chips and 800 nm cutting-edge technology and that was the time when countries like Taiwan and China could not even think of competing with India in this sector. In 1989, when a major fire incident broke out in the plant, the country suffered a massive setback. The mysterious fire ruined billions of dollars worth imported equipment and there was a colossal loss of Rs 60 crore.”
“This is when India’s dream of leading the semiconductor industry shattered into pieces. The intelligence bureau carried out a detailed investigation, but the reasons are yet to be revealed. If all these companies survived until now then, the country could have been the leading destination of chip manufacturing design and there would be no dependence on China, Taiwan, South Korea, and Vietnam,” added Kawoosa.
A media portal, Organizer Weekly, clearly stated that the UPA government never took the matter seriously of growing the semiconductor industry. Numerous global companies started operating their units in the southern parts of India in 2005, but these companies faced immense challenges in terms of the manufacturing equipment as they were to be imported from the US. In the end of 2013, the World Semiconductor Council penned a letter to the then government for possible cooperation. There were no subsidies and incentives given by the government to these companies and moreover, a huge import duties were also charged. This is when China again played the game of monopoly business and capitalized on this front by providing all kinds of financial assistance to global companies to start manufacturing in their country.
In an effort to meet the escalating demand, both European and the US semiconductor firms have carefully analyzed the Indian design talent and used the facilities in Taiwan for mass production, claims science commentator Dinesh C. Sharma. SCL, again failed to fully commence its manufacturing facility again, but nonetheless during the time of technological proscription, the company started producing chips for strategic ventures in defense and aerospace. Basically, after 1989, the business dynamics have altered all over the globe and the fact is that technology and equipment in this industry changes very rapidly. In India, the in-house demand was very poor and ample investments were not being provided.
Highlighting the historical aspects of India’s semiconductor industry growth, Minister of state for skill development & entrepreneurship and electronics & IT Rajeev Chandrasekhar ahead second edition of Semicon India 2023 event told the media that India missed the semiconductor bus due to lack of vision, clear strategy, and clarity by the previous governments. Speaking to the media prior to the conference, the minister added that the current government has made a lot of progress in this sector.
How India Is Now Aiming To Lead The Chip Manufacturing Race In The Coming Ten Years
After monitoring and analyzing the current challenges, the US based global firm Intel back in 2014 ignored to set-up its production unit in the country. Then, the government has started unleashing various schemes such as Scheme for Promotion of Manufacturing of Electronic Components and Semiconductors (SPECS), National Policy On Electronics (NPE), Modified Special Incentive Package Scheme (M-SIPS), and the much-awaited semiconductor incentive scheme of Rs 76,000 crore has been approved by the government back in December 2021 to boost semiconductor industry growth.
According to a previous report of CircuitDigest, the government has earlier notified that they are likely to approve another Rs 25,000 crore scheme to grow chip manufacturing. Under the Modified Semicon India Program, the fresh new applications were being invited by the union government from Jun 1, 2023 onwards in an effort to grow the nation’s display and semiconductor fabs. India Semiconductor Mission (ISM) will receive the applications and is tasked with leading the nations’ $10 billion semiconductor manufacturing program.
On Jul 21, 2023, in a written response to the Rajya Sabha, Rajeev Chandrasekhar has approved the beginning and restructuring of SCL Mohali again and he aims to turn it into a brownfield semiconductor manufacturing facility. And on the same day, the Odisha cabinet ministry has also approved the state’s semiconductor manufacturing and fabless policy by which the state cabinet is looking forward to magnetizing global investors and set-up electronics/chip manufacturing unit in the eastern front of the state. Speaking of this policy, the state is anticipating at least one chip producing unit and scores of fabless design operations.
Other than this, Rapidus Corporation, Japan's chip manufacturing firm has formed an MoU with the Indian government recently and then as per the recent report of the Economic Times, HCL group has also proclaimed its intention to set-up an assembly, testing, marking, and packaging (ATMP) unit with an investment around US$200-300 million. Now, although Foxconn canceled its $19.5 billion JV with Vedanta, both the companies announced plans to form its own chip unit. And last but not least, the US based Micron Technology has finally signed an agreement with the Gujarat government for setting-up a chip production facility with an investment of US$2.74 billion. The manufacturing unit will commence its operations in just eighteen months and it will provide direct employment to 5,000 people.
Speaking of the semiconductor growth in the coming decades, Amrit Manwani, managing director at Sahasra Group of Industries said, “The semiconductor industry is growing in India at an extraordinary level. By the end of 2026, the chip market in the country will reach around 55 billion that will augment at a CAGR of 20 percent from the period between 2022-2026. Now, speaking of the historical factor, the growth rate could have been tripled if we could have maintained that momentum and pace from the early 70s. As an entrepreneur I feel during that time, there was a lack of education and programs about how important industry electronics and semiconductors are in the future.”
Conclusion
When we speak of India turning into a global manufacturing hub for chips, there is a huge scarcity of talent and skilled workforce. And obviously, the period after 1987 until 2014 was a big hindrance in boosting the growth of the industry. The nation has faced various challenges in setting-up fabrication facilities required for large scale manufacturing. Now, with the increased pace of digitization and the growing demand for electronic products, India is still a huge importer of computer and memory chips and a couple of industry insiders have opined that the country is investing more on chip imports than oil. Obviously, to decrease that import reliance, India must find ways to develop semiconductor manufacturing for which both the union and the state governments must unveil impeccable policies, infrastructures, initiatives, and schemes crafted for scalable manufacturing. In order to meet the same, the nation can carefully analyze the case studies of the Asian country markets.