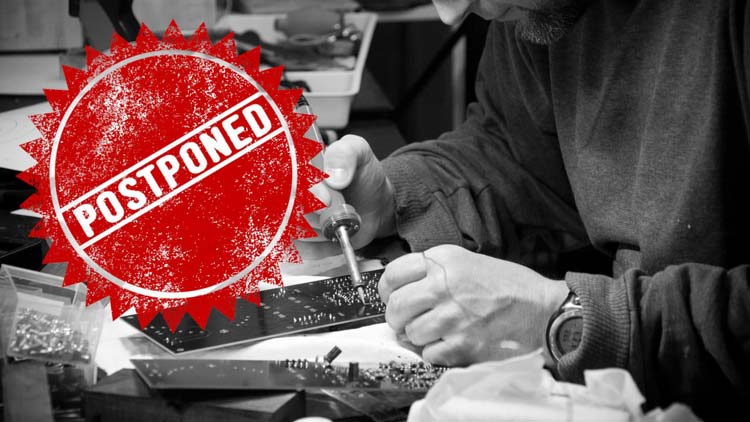
Take a moment and think of the last project you worked on. How many things didn’t go as planned? How many delays did the project experience in each phase and how could they have been avoided? Delays in any schedule are frustrating; when they happen in electronics project development, it can easily lead to a startup losing its edge in the market. Rightfully, this is of major concern (or at least it should be) to hardware developers and startups. Unfortunately, electronics project development delays are something founders and developers of all experience levels encounter during just about any given project.
In this article, we will go over the core causes of electronics project development delays, and then outline preventative strategies that have been effectively used in project management to help make the entire project sing.
Core Causes of Electronics Projects Development Delays
Every project has its ups and downs, good days and bad – but when we take a logical look into the mechanisms at work when schedule delays occur, we can see (hopefully only one of) seven factors at work:
1. Not DFM (Design for Manufacturing) – DFM is what should be at the top of mind during the manufacturing process because it is pivotal to the project’s success. DFM includes deciding specifics on the manufacturing process, product/part/board/chip design, materials used, environment, compliance/testing, and that barely breaks the surface of what DFM is all about. It’s so important that any aspect of hardware design not being DFM can cause even the most amazing projects to stall.
2. Certification Test Failures – Knowing that your hardware needs to pass certification is just the beginning here. The misunderstanding of which certifications the product needs to pass (e.g. EMI and EMC) or missing a requirement on certification for a different country can be extremely costly in regards to budget and schedule.
3. Design Changes from Testing Failures – During the development process, things can look great on paper but occasionally don’t work out so well when things move into test production. Many product defects are generally found after testing which requires developers to design changes. This takes significant time to resolve the issues and make trade-off decisions, e.g. to downgrade the specifications or change components (potentially increasing price).
4. Specification Changes – Often during the development process, you may receive new suggestions or feedback from customers which you want to implement immediately. However, these small changes here and there can have a ripple effect on your whole product design causing further delays and other work needing to be redone.
5. Out of Funding – For one reason or another, the money has dried up and the project can’t continue until more funding becomes available.
6. Out of Components – One (or more) of the hardware elements in your project is out of stock and has put your project on the shelf until more units are available.
7. No Recovery Plan – Otherwise known as ‘plan-b’, while everyone wants a project to succeed and go smoothly from start to finish, things can be put on hiatus if an unforeseen issue occurs and there’s no plan to fall back on.
While the above list gives many people reason enough to call it quits, nothing would get accomplished or created if everyone gave up. DON’T GIVE UP! You have a good idea and it should be seen through to production. Let’s look into how we can get you there.
Preventative Strategies Using Project Management
Proper prior planning prevents poor performance. In that vein and considering the core electronics project development delay causes outlined above, some of the top prevention measures you can take are fairly straightforward and easy to implement.
1. Make a strong commitment to make your project DFM – As outlined in the delay causes above, process, design, materials used, environment, and compliance/testing are just the beginnings of DFM. Define your specifications, pass it around to your team, talk to an expert, and lock it all down BEFORE approaching the manufacturer. Good DFM practices are the difference between a one-off and a scalable product. Work together with everyone involved to fill in ALL the blanks to ensure smooth and efficient manufacturing.
2. Plan ahead for certification testing by ensuring every step of the process is compliant, efficient, up to quality assurance standards. Be sure you understand which certifications the product needs to pass (e.g. EMI and EMC) as well as if there are different country certification requirements. In regards to budget and schedule, learning about quotations on certifications and sourcing is highly recommended.
3. Design changes from testing failures will be hard to completely avoid, but finding an experienced development/manufacturing partner who has experience with similar products in the past will reduce a lot of the risk. And for those problems that do arise, they will help provide workarounds and practical suggestions that will help you make quick decisions to avoid causing too much delay.
4. It sounds easy to say, but you must commit to locking down your specifications before getting too far into development. Save your new features for the next generation product. Unless it will make or break your product, it’s best to just get your product out there rather than spend eternity in development trying to perfect it.
5. Prevent running out of funds by planning ahead and creating a logical, reasonable, and feasible budget. Excel is your best friend here, list everything out, and arrange it to make sense for you and your project. Think of and make lists for things like NRE (Non-recurring Engineering) costs, BOM (Bill of Materials) costs, logistics, and anything else your project includes. It sounds like a no-brainer, but consulting to get a quote from an expert if you’re not sure about your numbers is a smart move and can actually save you time in the long run. They can help take a lot of pressure and stress off of your shoulders if you’re struggling to budget.
6. If your electronics project requires multiple parts and/or large quantities of parts, plan ahead and either source more than one supplier for the parts or hold extra stock – that way you’ll have a backup if the main source dries up. In addition, stay away from unique or specialized parts as they are likely to have longer lead times and will be harder to replace if any issues occur.
7. Any experienced project manager understands risk control, and making recovery plans during the project development cycle is part of their standard operating procedure. Proper project management can be so effective in preventing unforeseen delays.
Understanding what could go wrong is the first step in preventing that from happening. The second step is making a plan to either stop it from happening or work around it if it does. Proper prior planning prevents poor performance every time.
Communicate Your Electronics Project Development Plan
Communicate with outside experts to help ensure your specifications are clear and comply with DFM standard practices to ensure the best manufacturing experience and results possible. Preventing delays in electronics project development (and many other things in life) come down to planning the entire process, talking it over with your team, and working with other professionals who have electronics project development experience and success.
This article was authored by TECHDesign from Taiwan which is a one-stop E-commerce platform that connects hardware innovators. More details can be found on the TECHDesign Author Page.