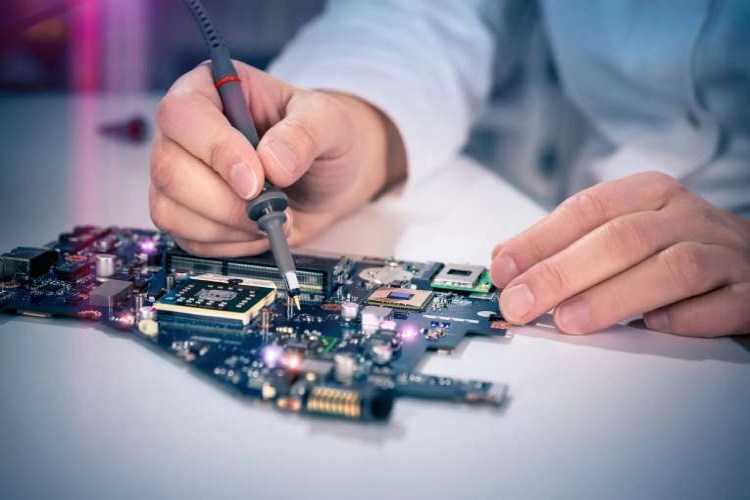
In the current product mix, out of the 100 billion dollars, we are actually manufacturing 52.7 percent of the electronics components, according to last year's data.
The union government, policymakers, and the manufacturers have been undertaking key initiatives to boost the country’s electronics and semiconductor manufacturing ecosystem. In an effort to position India as a global hub for ESDM and semiconductor manufacturing, the Production Linked Incentive Scheme (PLI) for large-scale electronics manufacturing, IT Hardware, Scheme for Promotion of Manufacturing of Electronic Components and Semiconductors (SPECS) and Modified Electronics Manufacturing Clusters Scheme (EMC 2.0) have been unleashed. In fact, the government has unleashed the most promising incentive scheme of Rs 76,000 Crore to attract investments from major semiconductor players. With the help of these schemes, India's electronics export is expected to reach $120 Bn by FY26. During April-November 2023, electronic goods exports were recorded at $17.74 Bn as compared to $14.36 Bn during April-November 2022, registering a growth of 23.56 percent.
According to some industry leaders, who wished to be unnamed, stated that around 30 years back, numerous electronic companies were not able to manufacture any kind of components because of the high restrictions imposed by the government in the industry. After every three months, manufacturers had to go to New Delhi to procure a new license for raw materials. The authorities during the late 90s even argued that India must focus on building software and let China lead the manufacturing ecosystem. In this regard, N Ramachandran, Managing Director, Mel Systems and Services Ltd, feels that the negative situation has changed dramatically because the government is now very proactive in supporting the industry.
Ramachandran said, “We need real support for infrastructure and existing industries. No small-scale unit can start an operation by purchasing land especially in cities like Chennai and this is because the price of land is more than their ability of investment. They cannot move to other smaller locations because their customer base, infrastructure, and manpower is located within the city. The level of subsidies is still inadequate in terms of components manufacturing. This is because they have higher investments, and the margin is very low. There is a requirement of additional PLI in areas such as PCBs and other components where the margins are very low.”
Speaking of the current challenges and prospects of India’s ESDM industry, Shri S Krishnan, IAS, Secretary MeitY feels that previously, the department was not looking to develop the core electronics and the focus was mostly centered upon developing software, e-governance and other aspects. Currently, 70 percent of PCBs used in India are still imported. But, in the past 5-6 years, the core electronics mojo is back again on the right track. India is now having a very successful PLI on IT hardware and 27 companies have signed MoUs. Many of them have already started operating. This PLI offers benefits even to the existing companies and provides subsidies as well. The overall projected investment is only about Rs 2,500 Crores.
In an effort to counter the grave impediments, industry insiders mentioned that as India now competes in the global electronics market, sustainability has to be the core business strategy. All the major manufacturers including both the giant companies and MSMEs must look into sustainability deeply, and start transforming the major source of their unit’s energy into green energy. Most importantly, these sectors need to create more employment, which can fulfill the dreams of the youth and make them more passionate to do something for their own country. For instance, Tata group has also invested Rs 2000 crores in the ITIs, which can be used for upskilling and reskilling. The industry has to come forward and form partnerships with all the stakeholders.
Amid all the challenges associated with the industry, how India can fulfill the mission of achieving the target of $300 billion by 2025-26. Managing Director of Deki Electronics, Vinod Sharma said that it is not that easy to achieve that target even in the coming four years. Sharma said, "I am not pessimistic about the target, but if 2.4 trillion dollars of electronics is divided by 8 billion population, then there will be $300 per capita consumption of electronics. We will definitely reach that target in a short period, but in the three years it seems difficult. Companies, which are not preparing for that target will definitely be left behind. In the current product mix, out of the 100 billion dollars, we are actually manufacturing 52.7 percent of the electronics components, according to last year's data."
“When we reach or close to reaching the target of 300 billion dollars, 150 billion dollars of components will be required, which is a little more than the amount of oil we are importing today. In fact, a week back, the nation imported more sensors than PCBs. Therefore, we need to chalk out a clear strategy to increase the volume of exports and reduce the key imports, and find out ways to escalate the value addition,” added Sharma.
Speaking of the future prospects of growth in the market, Richard Puthota, Senior Director Business Development at MacDermid Alpha Electronics Solutions mentioned that when customers are manufacturing different products, it helps to understand what kind of markets are emerging in the country. With the global engagements with major OEMs, the picture is crystal-clear where the industry is moving forward. When decisions are being made for the coming five years, developing technology is not the sole priority, but the numbers and the growth rate must be taken into consideration.
Richard said, “EVs in automotive segments will help us in achieving huge growth numbers. In fact, the customs duty imposed on white goods appliances will also give us a huge number. From the technology side, IoT and cloud computing will play a significant role in boosting the growth of this industry and most importantly, the telecom sector will add huge value addition in the electronics industry. India’s export of electronics is going to reach 120 billion by the end of 2026. The biggest advantage of India is that it is leading in both production and consumption. Speaking of the FAME scheme, both state and the central governments come up with sales penetration of 80% on two and three wheelers, 30% on private cars, 70% commercial cars, 40% buses by 2030.”
Around ten years back, there was no possibility for India to contribute to the ESDM and semiconductor value chain. The imperative aspect is that India is already doing a lot of design on semiconductors, but they are done for international companies, which will cater to the benefit of that particular country. It is now high time for the country to start doing design for itself. Now, the manufacturing area is a huge one and is about building a fab or an OSAT. There are a lot of procedures involved and India is nowhere in that ecosystem.
Speaking on the contribution in the value chain Mr. GS Madhusudan, Co-founder and CEO, Incore Semiconductors Pvt Ltd. said, “It’s not about the technical talents and we have dozens. For instance, when the US asks us to develop or do a design, we do it. 30-40% of designs happen outside India. Extensive product knowledge is lacking among us. We have an advantage as we are having huge consumers of the products. India should actually focus on parts costs between 50 cents to 5 dollars because most of the consumption will be in this range. We have to build older node products such as compound semiconductors, power IGBTs, RF with older technology and if we do that, I think India can supply between 10-15 percent of the world’s demand.”
Industry experts even feel that developing automation is the urgent need of the hour for the progress of India’s manufacturing industry’s growth. India must look at it as a lens of maximizing efficiencies, minimizing rejections and at the same time, bringing consistency and improving the quality. Consistency can only come from automation and scale. For India to become a global hub for manufacturing electronics, automation becomes extremely important. But the point is how, when, and at what cost.
Speaking of the challenges and growth of automation in industry, Ms. Nandini, Director at Tescom Pvt Ltd. said, “Msmes face the biggest challenge in deploying automation. We do not have a proper training center and costs are huge. Therefore, we start training workers when they join the organization. But, after 1-2 years, the workers start looking for jobs in a bigger organization. People in inspection systems and in testing are in huge demand and these are the areas which need to be automated. So, in our SMT line, almost everything is automated, but post SMT activities also need to get automated within the timeframe of two years. If it’s delayed, we will definitely miss the bus.”
Sasikumar Gendham - Managing Director at Salcomp Manufacturing India Private Limited and Vice-President at ELCINA opines that ‘Rome was not built in a day.’ Therefore, India will also become a global powerhouse of manufacturing in the coming few years. But, without developing automation and digitization, there is no way India can succeed in electronics manufacturing globally.