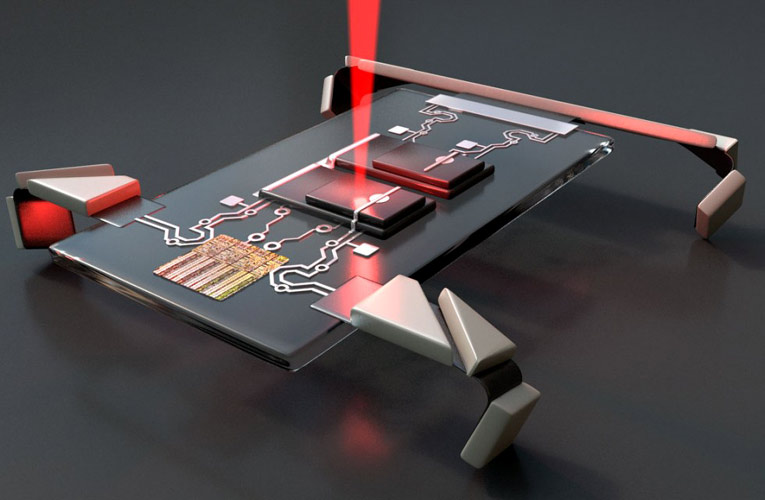
There has been ongoing research taking place over the decades to develop an actuator at micrometer resolutions that can work with semiconductor processing and can be triggered using conventional electronic signals. The rudimentary microscopic robots have been developed, but all of them have limited functionality as conventional silicon electronics have not been used efficiently. However, the researchers from Cornell University have been successful in creating millions of sub-hundred-micrometer walking robots that operate with the help of conventional electronics.
The robots developed are so small (about the size of paramecium) that hundreds of them can simultaneously pass through a hypodermic needle. These robots have tiny photovoltaic panels that can be targeted by an external laser to give the robot commands. They feature four electrochemical actuators as legs that connect to silicon photovoltaics that serves as the processing center. Existing semiconductor technology has been used to make the robots’ brain small and releasable.
Each robot has extremely thin platinum strips that have a layer of titanium on one side. Upon applying a positive electric charge to the platinum strips, negative ions from the nearby environment show up and balance out the charge. The same ions cause the platinum to expand and flex the leg. Polymer chunks on the metal strips enable the creation of bending points, emulating the knees or ankles.
According to the researchers, the team has worked on making the robots compatible with standard microchip fabrication, thereby opening the door to making these microscopic robots smart, fast, and mass-producible. The team also added that a single 4-inch silicon wafer can be used to manufacture about one million of the new robots using existing lithography processes. These robots have successfully paved the way for building ever more complex microscopic robots that may one day be used in the human body. Further, the team plans to do electronic integration on these tiny robots.