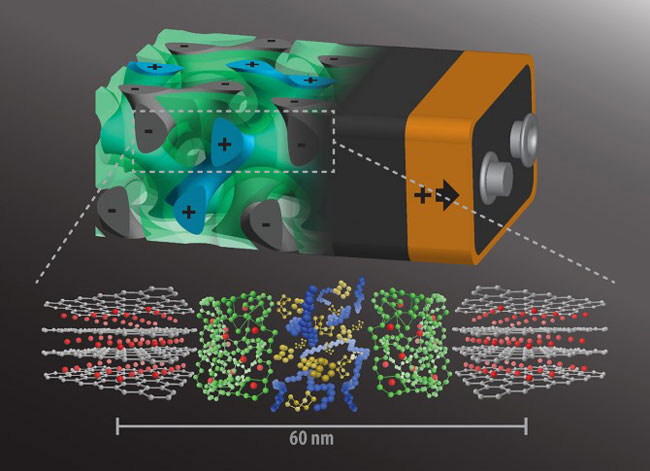
“There's never enough time to do all the nothing you want”, charging a battery make me feels like the same.
Researcher’s team at Cornell University led by Ulrich Wiesner, the Spencer T. Olin Professor of Engineering in the Department of Materials Science and Engineering, addresses the demand of a battery which has the potential of lightning-quick charges.
Idea behind this technology: “Instead of having the batteries’ anode and cathode on either side of a non-conducting separator, intertwine the components in a self-assembling, 3D gyroidal structure, with thousands of nanoscale pores filled with the components necessary for energy storage and delivery”.
“This is truly a revolutionary battery architecture,” said Wiesner, whose group’s paper, “Block Copolymer Derived 3-D Interpenetrating Multifunctional Gyroidal Nanohybrid for Electrical Energy Storage,” was published May 16 in Energy and Environmental Science, a publication of the Royal Society of Chemistry.
“This three-dimensional architecture basically eliminates all losses from dead volume in your device,” Wiesner said. “More importantly, shrinking the dimensions of these interpenetrated domains down to the nanoscale, as we did, gives you orders of magnitude higher power density. In other words, you can access the energy in much shorter times than what’s usually done with conventional battery architectures.”
How fast is that? Wiesner said that, due to the dimensions of the battery’s elements being shrunk down to the nanoscale, “by the time you put your cable into the socket, in seconds, perhaps even faster, the battery would be charged.”
This 3D-battery’s concept is based on block copolymer self-assembly, which they used to employ in other electronic devices includes a gyroidal solar cell and a gyroidal superconductor. Lead author of this work, Joerg Werner experimented with self-assembling filtration membranes and wondered if that principle could be applied to carbon materials for energy storage.
The gyroidal thin films of carbon – the battery’s anode, generated by block copolymer self-assembly – featured thousands of periodic pores on the order of 40 nanometers wide. Further coating these pores with a 10 nanometer-thick, which is electronically insulated but ion-conducting separator were coated through electro-polymerization, which by the very nature of the process produces a pinhole-free separation layer. And, absolutely these defects like holes in the separator can lead to catastrophic failure giving rise to fires in mobile devices such as cell phones and laptops.
The move to the second step, which is an addition of cathode material. In this case, add Sulphur in an appropriate amount that doesn’t quite fill the remainder of the pores. But, sulfur can accept electrons but doesn’t conduct electricity. The final step is to backfilling with an electronically conducting polymer, known as PEDOT (poly [3, 4-ethylenedioxythiophene]).
While this architecture offers proof of concept, Wiesner said, it’s not without challenges. Volume changes during discharging and charging the battery gradually degrade the PEDOT charge collector, which doesn’t experience the volume expansion that sulfur does.
“When the sulfur expands,” Wiesner said, “you have these little bits of polymer that get ripped apart, and then it doesn’t reconnect when it shrinks again. This means there are pieces of the 3D battery that you then cannot access.”
The team is still trying to perfect the technique but applied for the patient protection on the proof-of-concept work. The work was supported by Energy Material Center at CORNELL and funded by U.S. Department of Energy as well as National Science Foundation.